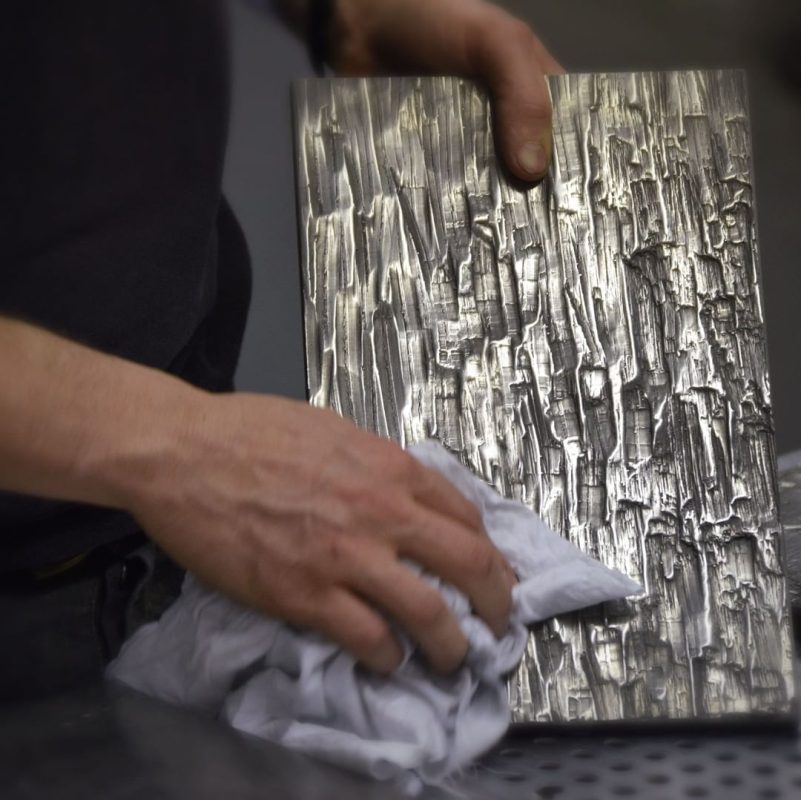
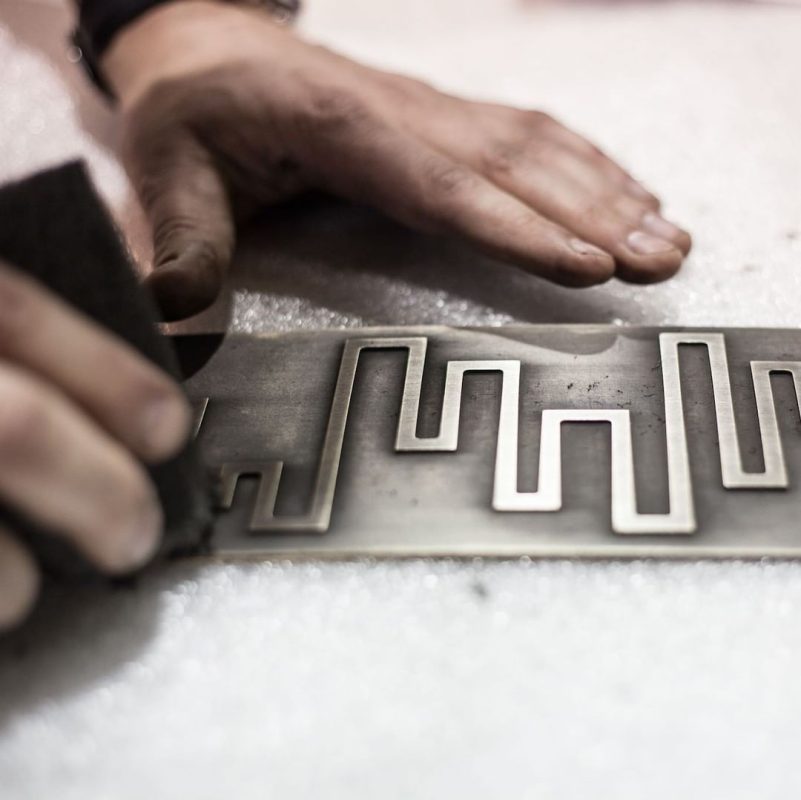
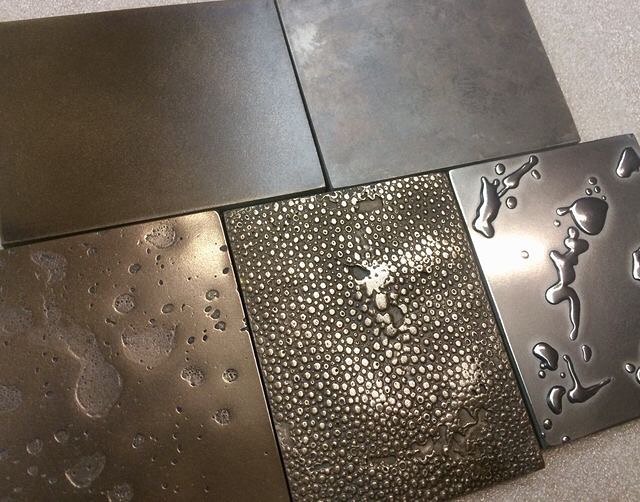
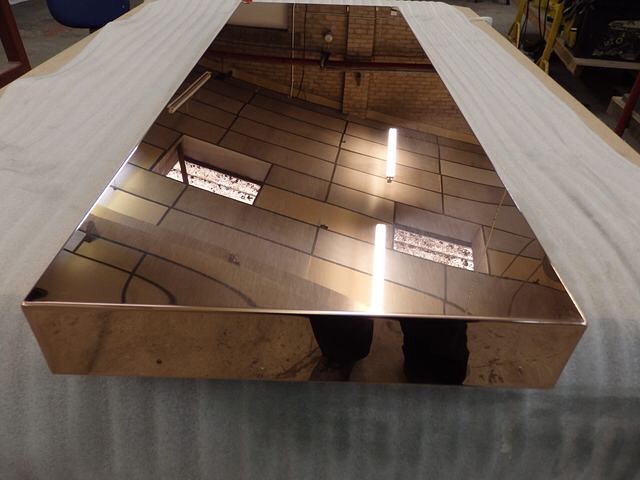
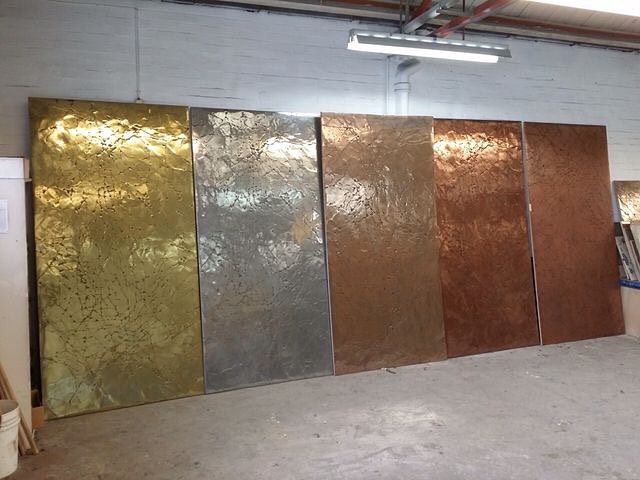
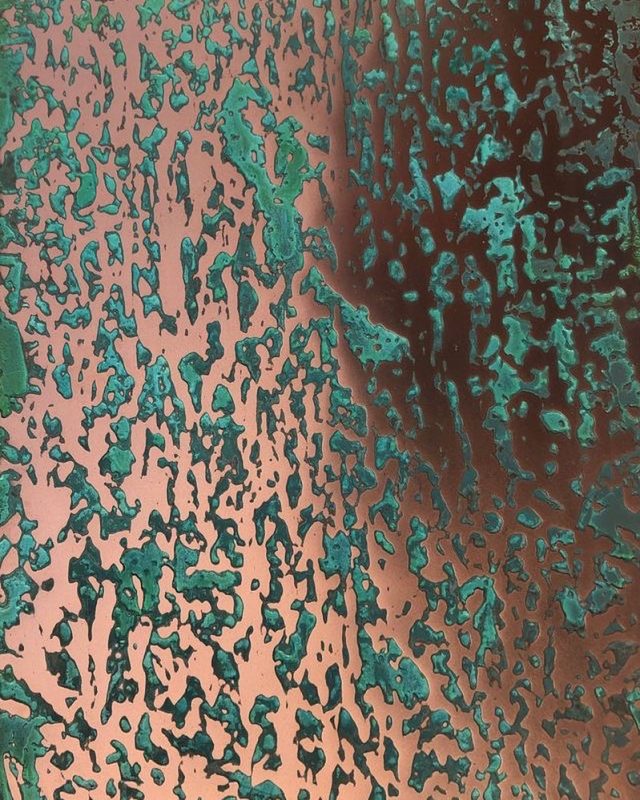
Did you know that liquid metal coatings, a type of metallic paint, can reduce friction by up to 80% through surface metallization with different metals? This innovative technology, including versatile surface coating and liquid metal products, is changing the game in various industries with solid metal and its effect. Liquid metal coating, a product of metalier coatings, offers a sleek, durable finish that protects surfaces from wear and tear, creating a metallic paint effect. It’s not just for aesthetics; it enhances performance too.
From automotive parts to electronics, this premium metal finish coating provides unmatched resistance to heat and corrosion with a real metal finish. Businesses are increasingly turning to liquid metal solutions for their reliability and efficiency as a product of surface coating, powder coating, and metallic paint. Understanding what liquid metal coating and metallic paint are, and how they work, can help you make informed decisions for your projects. Dive into the world of metallic paint and liquid metal coating and discover its benefits today.
Key Takeaways
- Liquid metal coating is a unique metallic paint that provides strong protection and aesthetic appeal for various surfaces.
- It is made from a blend of metals and metallic paint, which gives it its distinctive liquid-like properties and durability through powder coating and surface coating.
- This coating, which includes metallic paint and metal finishes, can be used in industries like automotive, aerospace, and construction, showcasing its versatility with a real metal finish.
- Beyond protection, metallic paint liquid metal coatings enhance the appearance of products, making them visually striking.
- While there are many advantages, such as corrosion resistance with powder coating and decorative metal coating systems, consider potential downsides like cost and application complexity in liquid metal coating solutions and other metal finishes.
- Explore alternatives if liquid metal coating doesn’t fit your needs, as there are other effective protective coatings available.
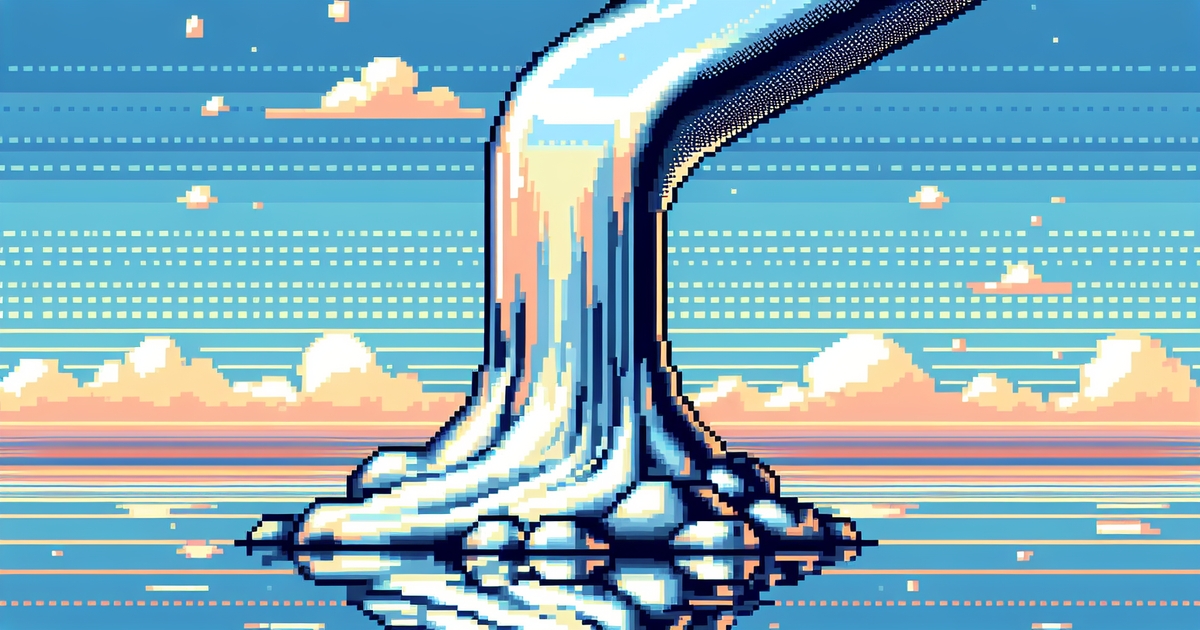
Understanding Liquid Metal
Definition and Basics
Liquid metal coating is a real metal coating that contains about 95% metal powder. This high concentration gives it unique properties. It can be applied to various surfaces like wood, plastic, and metal using powder coating and liquid metals. Once applied, it creates a durable finish. The coating mimics the properties of cast metal. It provides strength and resistance to wear.
Liquid metals can also conduct heat and electricity well. This makes them useful in many industries. They are not just for decorative metal coating but serve practical purposes too, including metal finishes, metal paint, and a real metal finish.
History and Development
The technology for liquid metal coatings has evolved significantly over time. It began in the early 2000s when researchers explored new ways to use metal powders and liquid metals. In 2005, key developments led to commercial applications. Companies started using liquid metal coatings in automotive and aerospace industries.
By 2010, advancements allowed for better adhesion and durability. These improvements expanded its applications beyond industrial uses. Home improvement projects began to adopt liquid metal coatings for aesthetic purposes. Today, these coatings with a real metal finish are popular in art and design as well.
Common Types
There are several types of liquid metals used in coatings. Some common examples include liquid copper, aluminum, and silver. Each type offers different benefits based on its properties.
Finishes vary widely with liquid metals. They can be matt, shiny, or textured depending on the desired look, such as a real metal finish, decorative metal coating, powder coating, or liquid metal coating solution. Some people even choose rusted or patinated appearances with a decorative metal coating for a vintage style. These variations allow for creativity in design.
Liquid metal coatings provide options for both functional and decorative uses. They enhance surfaces with decorative metal coating while offering durability and resistance to elements through powder coating, real metal finish, and liquid metal coating solution.
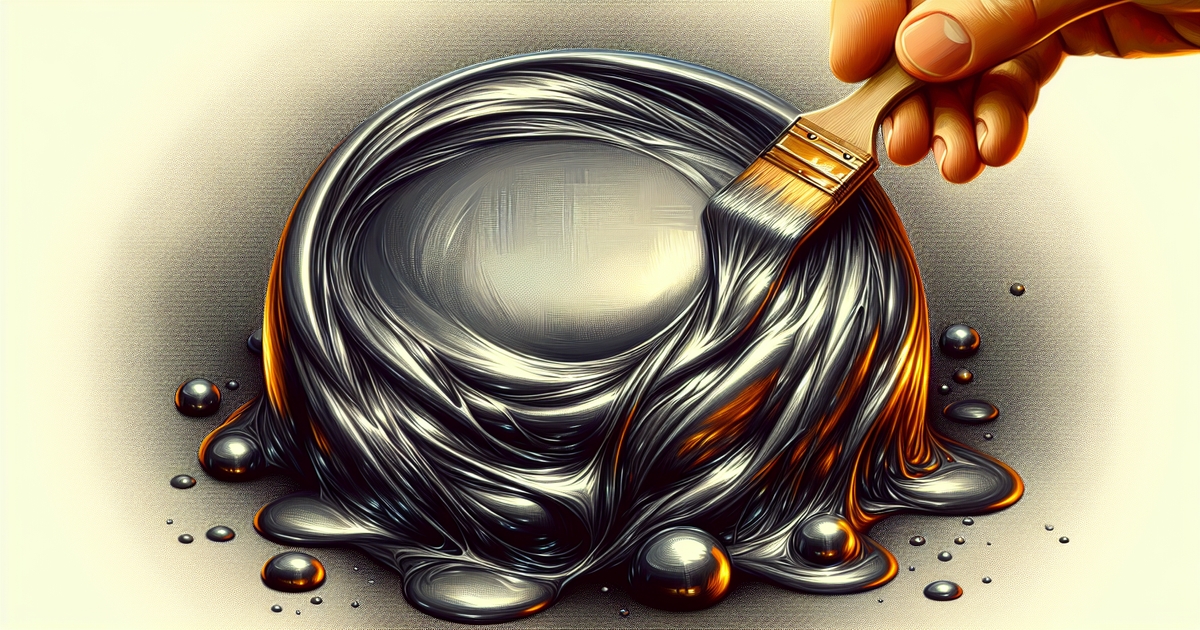
Composition of Liquid Metal Coating
Key Ingredients
Liquid metal coating primarily consists of metal powder and binding agents. The metal powder can include aluminum, zinc, or other metals. These powders provide the metallic finish and properties of the coating. Binding agents help to adhere the metal particles to the surface being coated in powder coating.
Additives play a crucial role in achieving specific finishes. For example, certain additives can enhance gloss or improve scratch resistance in a decorative metal coating, a real metal finish, or a liquid metal coating solution. The quality of these ingredients is vital for durability. High-quality materials lead to longer-lasting coatings with a real metal finish that withstand wear and tear.
Manufacturing Process
The manufacturing process of liquid metal coating involves several key steps. First, surface preparation is essential. This step cleans and primes the surface with a liquid metal coating solution to ensure proper adhesion for the decorative metal coating. After preparing the surface, the liquid metal coating solution is applied.
Curing occurs after application. This stage allows the coating to harden and bond effectively with the surface. Sanding may follow curing to achieve a smooth finish. Optional processes such as aging or brushing, along with decorative metal coating or liquid metal coating solution, can add texture. These techniques create unique visual effects on the final product using a liquid metal coating solution.
Chemical Properties
Liquid metal coatings exhibit strong chemical stability. They resist corrosion and oxidation, making them suitable for various environments, including a liquid metal coating solution. This resistance is crucial for applications exposed to moisture or harsh chemicals, such as a liquid metal coating solution.
e liquid metal coatings may react with environmental factors like UV light or extreme temperatures. Understanding these reactions helps in selecting the right coating for specific applications. Proper selection ensures optimal performance and longevity.
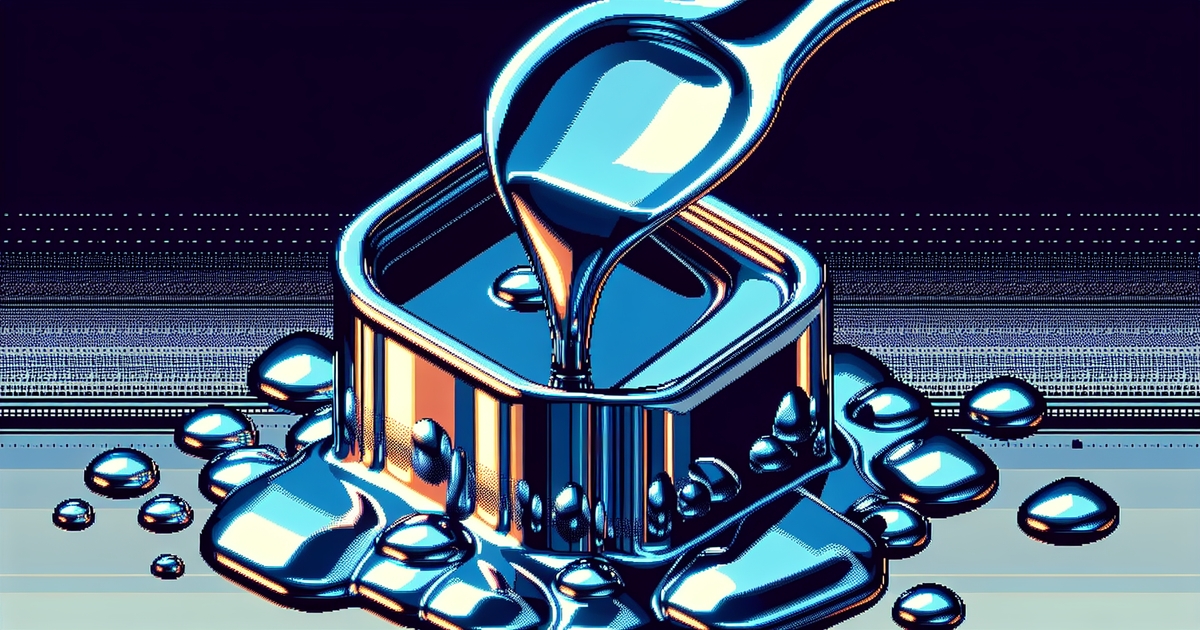
Properties of Liquid Metal Coating
Durability and Strength
Liquid metal coatings are known for their long-lasting nature. They resist physical wear and tear better than many other coatings. This durability means they can withstand harsh conditions without degrading. Their strength is comparable to solid metal surfaces. This makes them ideal for applications where toughness is essential. For example, industries that deal with heavy machinery benefit greatly from these coatings. They help protect surfaces from scratches and dents.
Heat Resistance
High-temperature tolerance sets liquid metal coatings apart. These coatings can handle extreme heat without losing effectiveness. They are suitable for environments with fluctuating temperatures. This makes them perfect for use in automotive and aerospace industries. In these fields, materials often face intense heat from engines or external conditions. Liquid metal coatings ensure that components remain intact and functional even under stress.
Conductivity
Liquid metal coatings offer excellent electrical conductivity. This property allows them to be used in various electronic components. Devices like smartphones and laptops can benefit from this feature. The coatings help improve performance and efficiency in electronics.
Thermal conductivity is another significant advantage of liquid metal coatings. They assist in heat dissipation, which is crucial for preventing overheating in electronic devices. Proper heat management keeps devices running smoothly and extends their lifespan.
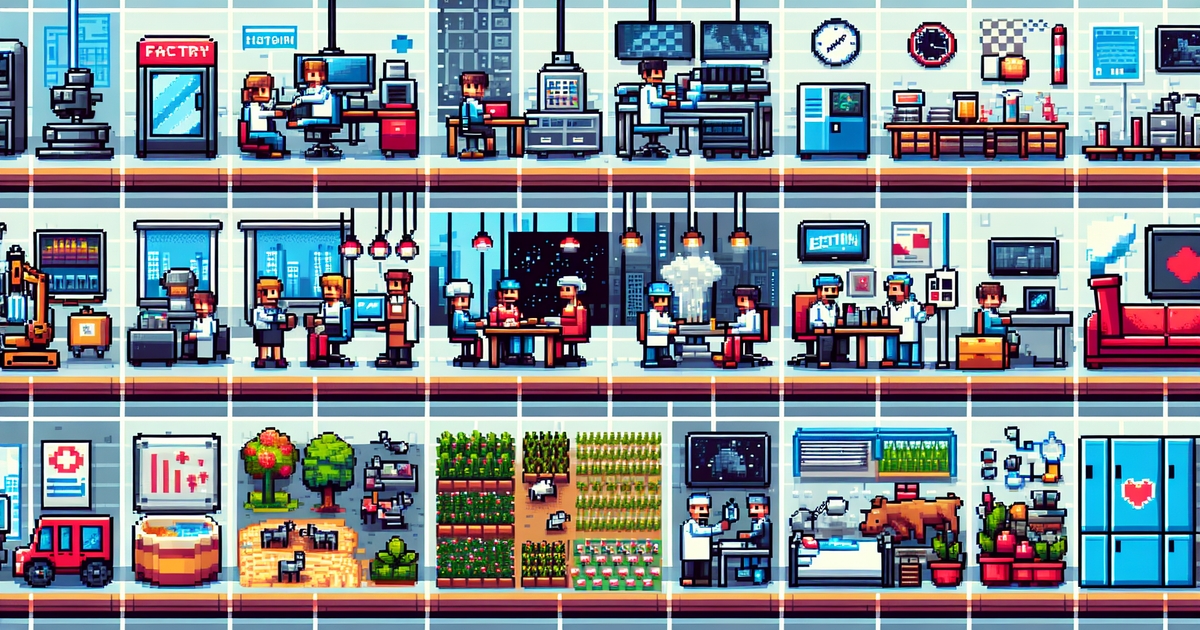
Uses in Various Industries
Automotive Applications
Liquid metal coating has several uses in the automotive industry. Car manufacturers apply it to both interiors and exteriors for improved aesthetics. The shiny finish enhances the visual appeal of vehicles.
This coating also provides protective benefits against environmental elements. It helps resist corrosion, scratches, and UV damage. Cars last longer and maintain their appearance better with this protection. Liquid metal allows for more flexibility in vehicle design. Manufacturers can create unique shapes and styles that were difficult to achieve before.
Electronics and Technology
In electronics, liquid metal coating plays a vital role. It is commonly used in circuit boards and connectors. This application improves conductivity, which can enhance overall device performance.
Innovations in wearable technology also benefit from liquid metal. For instance, researchers are exploring its use in flexible displays and sensors. These advancements could lead to lighter and more efficient devices. Liquid metal’s unique properties make it an exciting option for future tech developments.
Construction and Architecture
The construction industry utilizes liquid metal coating as well. It is effective for building facades and various interior design elements. This material creates visually appealing surfaces that stand out.
Benefits include the ability to create seamless architectural features. Liquid metal can fill gaps, making structures look sleek and modern. Moreover, it enhances structural aesthetics without sacrificing durability or functionality.
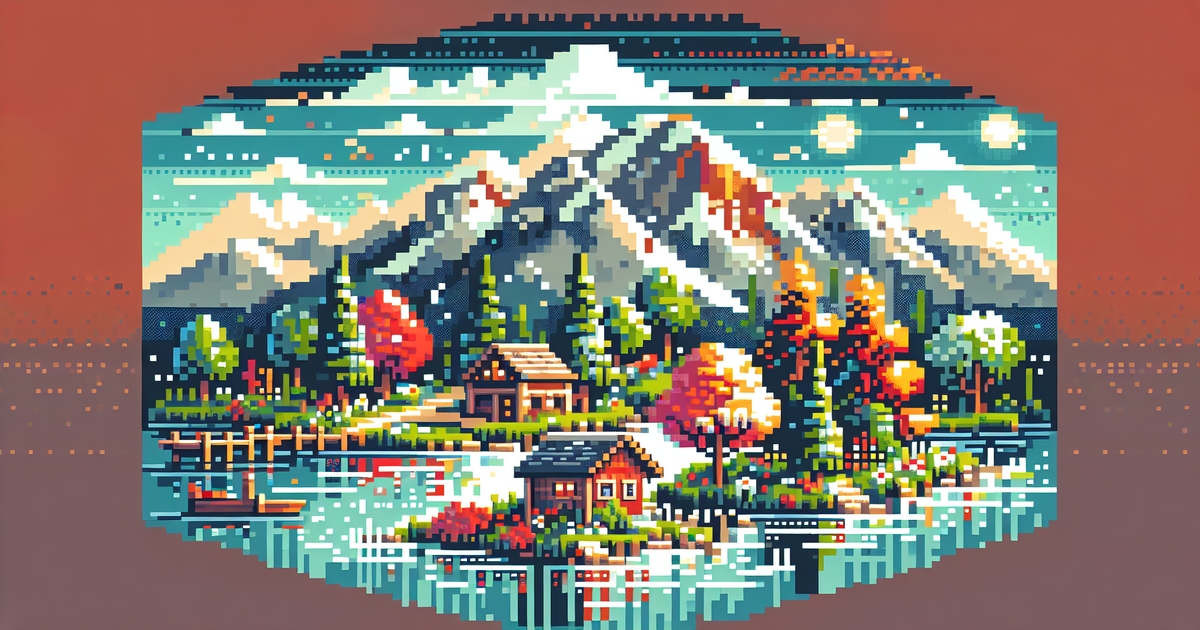
Decorative and Aesthetic Benefits
Design Flexibility
Liquid metal coatings offer extensive customization options for unique designs. Users can create specific looks that match their vision. This flexibility allows for adaptation to various shapes and forms. Whether the surface is flat, curved, or complex, liquid metal can conform easily.
Intricate patterns are also achievable with this technology. Designers can replicate detailed textures and designs, making each piece one-of-a-kind. This capability enhances creativity in design projects.
Surface Finishes
Different textures are possible with liquid metal coatings. Users can choose from a range of finishes, including rough, smooth, glossy, or matte. The process to achieve these finishes involves careful application techniques.
Polishing plays a crucial role in the final appearance of the coating. A polished surface often appears more reflective and vibrant. In contrast, a matte finish provides a softer look. Each finish can significantly impact how the object is perceived.
Color Variations
A wide range of colors is available in liquid metal coatings. Users can select from standard colors or opt for custom hues to fit specific needs. Techniques like mixing pigments with the coating allow for endless possibilities.
The choice of color affects design and aesthetics greatly. Bright colors can draw attention, while muted tones provide elegance. Custom colors help align the finished product with branding or personal style.
Advantages of Liquid Metal Coating
Longevity and Maintenance
Liquid metal coatings require low maintenance. This makes them appealing for many users. They last longer than traditional coatings. Many standard coatings need frequent touch-ups. In contrast, liquid metal coatings resist wear and tear better.
Cleaning these surfaces is straightforward. A simple wipe with a damp cloth keeps them looking fresh. No special cleaners are necessary. This ease of maintenance saves time and effort for owners.
Lightweight Benefits
Liquid metal coatings add minimal weight to surfaces. This characteristic is crucial in many applications. Industries like aerospace and automotive benefit greatly from this feature. Lighter materials can improve fuel efficiency and performance.
Portable devices also gain from this lightweight advantage. Consumers appreciate lighter laptops and smartphones. The reduced weight enhances user experience without sacrificing durability.
Versatile Applications
Liquid metal coatings find use in various fields, including:
- Aerospace
- Automotive
- Electronics
- Medical devices
- Architecture
Their versatility allows for innovative solutions across industries. Companies can explore new ways to apply these coatings. For example, the medical industry can use them for advanced surgical tools.
Adaptability is a key strength of liquid metal coatings. As market needs change, these coatings can adjust accordingly. This flexibility opens doors for further innovation.
Disadvantages and Considerations
Cost Factors
Liquid metal coatings can be more expensive than traditional metalwork. The initial cost often includes specialized materials and labor. Material quality plays a significant role in the price. Skilled labor is necessary for proper application, which can add to expenses. However, these coatings may lead to potential savings in long-term maintenance. They resist corrosion and wear better than some traditional options. This durability can reduce the need for frequent repairs or replacements.
Environmental Impact
Liquid metal coatings offer eco-friendly benefits. They produce less waste compared to conventional metal processes. Traditional methods often involve cutting and shaping, which generate scrap metal. With liquid coatings, there is minimal leftover material. These coatings can be recycled and reused. This reduces the overall environmental footprint of manufacturing processes. Sustainable practices become easier with liquid metal applications.
Availability and Accessibility
Liquid metal coatings are widely available in many markets. Professionals can find them at local suppliers or specialty stores. DIY enthusiasts also have access to these products through online retailers. Many websites provide detailed information on various types of liquid metal coatings. This makes it easy for anyone to understand their options. Furthermore, tutorials and guides are readily available for those looking to apply these coatings themselves.
Alternatives to Liquid Metal Coating
Traditional Metal Coatings
Liquid metal coatings differ from traditional metal plating in several ways. Traditional methods often use electroplating. This process involves depositing a layer of metal onto a surface using electricity. Liquid metal coatings, however, apply a liquid alloy that solidifies on the surface.
Application techniques vary significantly. Liquid metal coatings offer a smoother finish. They can cover complex shapes more easily than traditional methods. This results in fewer imperfections and better aesthetics.
Durability is another key difference. Traditional metal coatings may chip or wear over time. They often require regular maintenance to keep surfaces looking good. In contrast, liquid metal coating suits various environments, providing longer-lasting protection with less upkeep.
Synthetic Coatings
Synthetic coatings present another alternative to liquid metal coatings. These materials are often made from polymers or plastics. They can mimic the look of metals but lack the same properties.
Authenticity is a major benefit of liquid metal coatings compared to synthetic options. Liquid metals provide a genuine metallic appearance. They reflect light like real metals do, enhancing visual appeal.
Environmental impact also varies between these options. Synthetic coatings can release harmful chemicals during production and disposal. Liquid metal coatings generally have a lower environmental footprint. They are safer for both users and the planet, making them an appealing choice for many applications.
Emerging Technologies
New advancements in liquid metal coating technology continue to emerge. Research focuses on improving application methods and enhancing performance. Innovations aim to make these coatings even more versatile.
Integration with smart materials is one exciting trend. Liquid metal coatings can be combined with sensors and IoT devices. This allows for real-time monitoring of the coated surfaces. For example, they can detect wear or damage and alert users before problems escalate.
Future trends suggest even more breakthroughs ahead. Companies are exploring ways to create self-healing liquid metal coatings. These innovations could revolutionize how we protect surfaces in various industries.
Closing Thoughts
Liquid metal coating is a game-changer in many industries. Its unique properties and aesthetic appeal make it a popular choice for various applications. You’ve learned about its composition, advantages, and even some drawbacks. Understanding these elements helps you make informed decisions for your projects.
Embrace the potential of liquid metal coatings to enhance your products and designs. Whether you’re looking for durability or style, this technology offers numerous benefits. Explore your options and consider how liquid metal can elevate your work. Dive deeper into this innovative solution today!
Frequently Asked Questions
What is liquid metal coating?
Liquid metal coating is a specialized surface treatment that uses a liquid metal alloy to enhance the properties of materials. It provides protection, durability, and aesthetic appeal.
How is liquid metal coating applied?
Liquid metal coating is typically applied using spray techniques or dipping methods. This allows for even coverage and effective bonding to the substrate material.
What industries use liquid metal coatings?
Liquid metal coatings are utilized in various industries, including automotive, aerospace, electronics, and construction. They improve wear resistance and extend the lifespan of components.
Are there any health risks associated with liquid metal coatings?
While generally safe, some liquid metal coatings may contain toxic elements. Proper safety precautions, such as using protective gear and ensuring adequate ventilation, are essential during application.
How does liquid metal coating improve durability?
Liquid metal coatings create a strong barrier against corrosion, abrasion, and heat. This enhances the longevity of the underlying material, making it suitable for harsh environments.
Can liquid metal coatings be removed?
Yes, liquid metal coatings can be removed using chemical strippers or mechanical methods. However, care must be taken to avoid damaging the substrate beneath.
What are the main advantages of liquid metal coating?
The primary advantages include enhanced durability, corrosion resistance, aesthetic appeal, and improved thermal conductivity. These benefits make it a popular choice across multiple applications.