Key Takeaways
- Epoxy resin is a versatile material with an incredibly strong bond. Its durability allows for ideal use during construction, art, and electronics.
- Epoxy resin consists of a resin and a hardener. Mix them together, and a chemical reaction occurs that produces an incredibly rigid and tough plastic.
- Always wear gloves and a mask when working with Epoxy Resin. Since mold is a health hazard, make sure your flat is well ventilated.
- To get the best results with epoxy resin, it’s all in the mix and cure. Accomplishing this means closely measuring ingredients and following curing times to the letter.
- When you compare epoxy resin to other resins, look for factors such as strength, flexibility, and resistance to the environment. These characteristics can drastically affect your resin choice for certain projects.
- Understand the properties and applications of epoxy resin to select the ideal type for your project. This knowledge ensures long-lasting, effective results.
Did you know the epoxy resin market value hit $8 billion in 2023? Crazy, right? So what’s up with epoxy resin? It’s this really useful stuff that you get when you mix two chemicals. You can find it in tons of places. Remember those shiny floors, the tough boat hulls, the cool looking art pieces?
However, while epoxy resin is incredibly useful. It’s safe as can be, but you’ve got to use it right. You’ve got to wear gloves and masks, for one. Ventilation is a big deal. You don’t want those fumes hanging around. It’s like talking with a friend about something awesome but useful. Get to the bottom of it, learn what it is, why it’s everywhere, and how to use it. Understanding epoxy resin isn’t just for the geeks. It’s actually for anyone who wants to know all the wonderful ways it simplifies life.
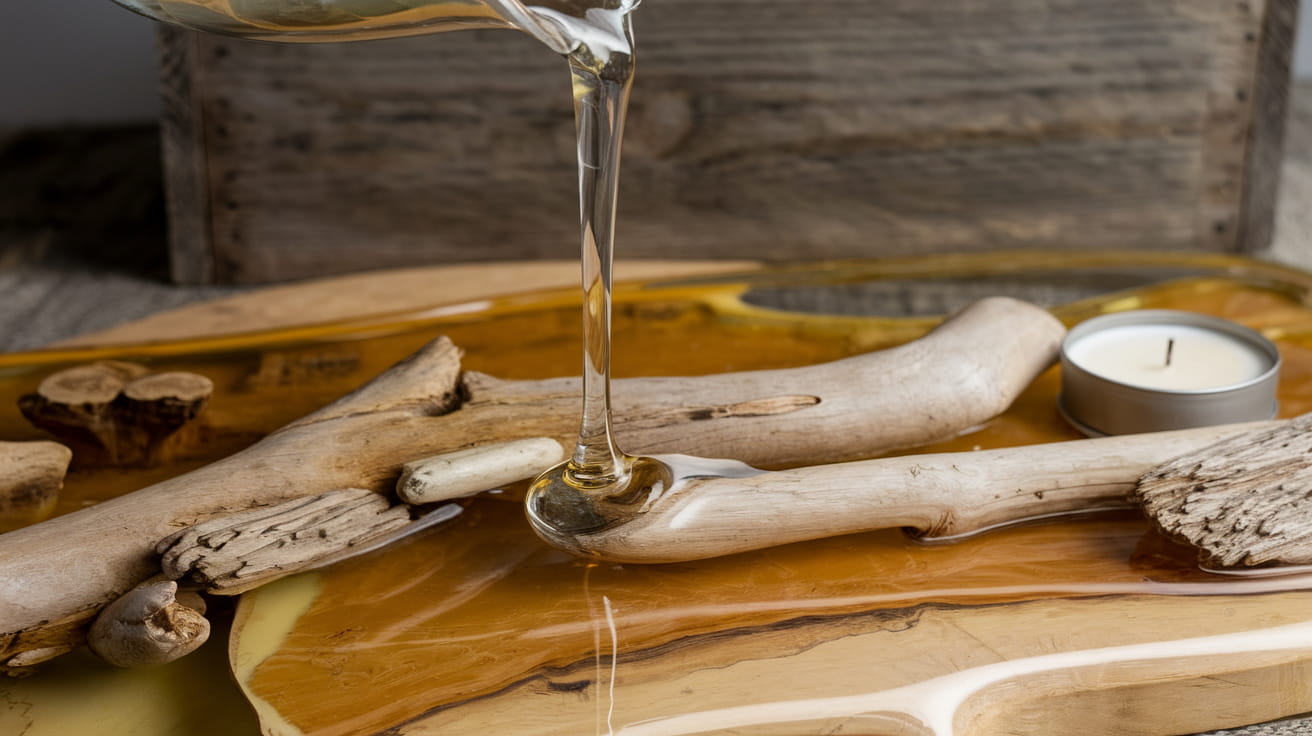
What is Epoxy Resin?
Definition and Composition
Epoxy resin, a useful adhesive material, enjoys popularity in many industries. What makes it tick? It’s basically a two-part system: you’ve got the resin and the hardener. When these two combine, they initiate a chemical reaction that converts them into a rock-hard structure. This reaction isn’t just some magic trick; it’s what makes epoxy resin so versatile and strong. The mix’s composition can be tweaked for different uses, like construction, woodworking, or even manufacturing. It’s this adaptability that enables epoxy to shine. If you’re looking for a resin that sticks like glue or one that stands up to the elements, your mixing method is critical. How you mix your resin and hardener will affect the outcome.
Properties of Epoxy Resin
Enough about what epoxy resin is; let’s discuss what epoxy resin can do. It’s got some wicked properties like crazy good adhesion that makes it stick to anything. It also has stellar chemical resistance, meaning it doesn’t break down easily. When it comes to durability, it’s built to last. Temperature swings are not an issue, with its thermal stability. When it comes to electrical insulation, epoxy is there to keep things safe and sound. These properties make it a superstar for applications like marine uses, wind energy components, and more. It’s a genuine Jack-of-all-trades.
Epoxy Resin Composition
Chemical Components
A handful of chemical components make up epoxy resin. The main compounds used are epichlorohydrin (ECH) and bisphenol A. When they react, they produce bisphenol A diglycidyl ether, or BADGE, or DGEBA. This substance is so important they even need it for epoxy resins. It has crucial epoxy groups — typically two to six per molecule — that give these resins their special character. The epoxy groups make up the proverbial magic ingredient in the chemical structure. They encourage the resin to create solid, long-lasting bonds.
Hardeners play a massive role in epoxy resin too. They assist in curing, which is when the liquid resin becomes solid. This reaction usually needs a precise mix of two components: the resin and the hardener. When combined, they create a new chemical structure delivering the strength and durability you need. Common additives like fillers and colorants can improve performance or attain particular qualities. These qualities, along with various options for curing methods, make epoxy systems very versatile.
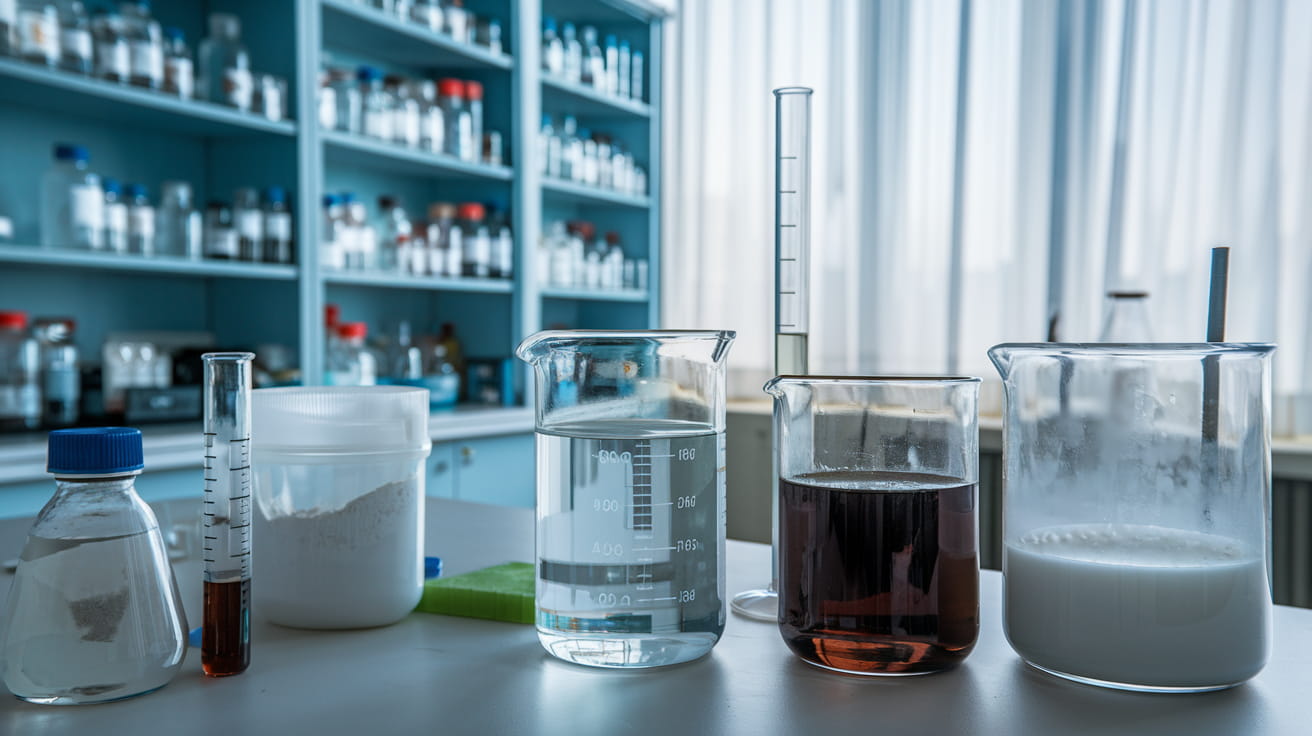
Types of Epoxy Resins
There are several types of epoxy resins, each with its own applications and benefits. The most common ones are bisphenol-based, aliphatic, novolac, halogenated, and glycidylamine resins. Each type serves different purposes:
- Bisphenol-Based Resins: Bisphenol-based resins are often used as they offer high strength and good chemical resistance. Widely commercialized resins include ones based on bisphenol A. Bisphenol F can also be used, which offers lower viscosity and higher chemical resistance. While they have many benefits, there are health issues associated with bisphenol compounds, so you need to be careful with your new purchase. These resins are commonly used in industrial applications, ranging from coatings to adhesives, highlighting their versatility.
- Aliphatic Resins: Of particular note are aliphatic epoxy resins, which are known for their flexibility and color stability. They resist UV light well, which means they don’t yellow over time, making them perfect for outdoor use. Though flexible, they are slightly less durable than other types. These resins are often used for automotive coatings and protective films for outdoor structures.
- Novolac Resins: Novolac epoxy resins are known for their unique properties, such as enhanced heat and chemical resistance. They’re also used in environments where these features are critical, such as in chemical plants or for high-temperature coatings. Novolac resins tend to be brittle and are often expensive. This brittleness and expense limit them to niche, demanding applications.
- Halogenated Resins: Flame retardancy is the hallmark of halogenated epoxy resins, rendering them indispensable in electronics and electrical components. They provide essential dielectric properties, making them safe and effective in these sensitive areas. Safety is a major consideration since halogens are involved. They can also pose significant environmental and health risks.
- Glycidylamine Resins: Glycidylamine resins are multi-functional with excellent thermal stability and mechanical properties. They’re frequently used in high-performance coatings and adhesives, where these qualities matter. In terms of resistance to harsh conditions, glycidylamine resins outperform other types of epoxy. This makes them an ideal fit for all types of intensive industrial applications.
Advantages and Disadvantages
Epoxy resin has its own set of perks and quirks. On the plus side, it has high adhesion and is water-resistant, perfect for the most demanding environments. Beware of its downsides, such as brittleness and the potential for yellowing over time. Understanding these pros and cons is the key to using epoxy effectively. When choosing the best type, consider what you want it to accomplish. Is it to last longer, to be more flexible, or for some other reason? Matching the resin’s properties to your project can be the difference.
Applications of Epoxy Resin
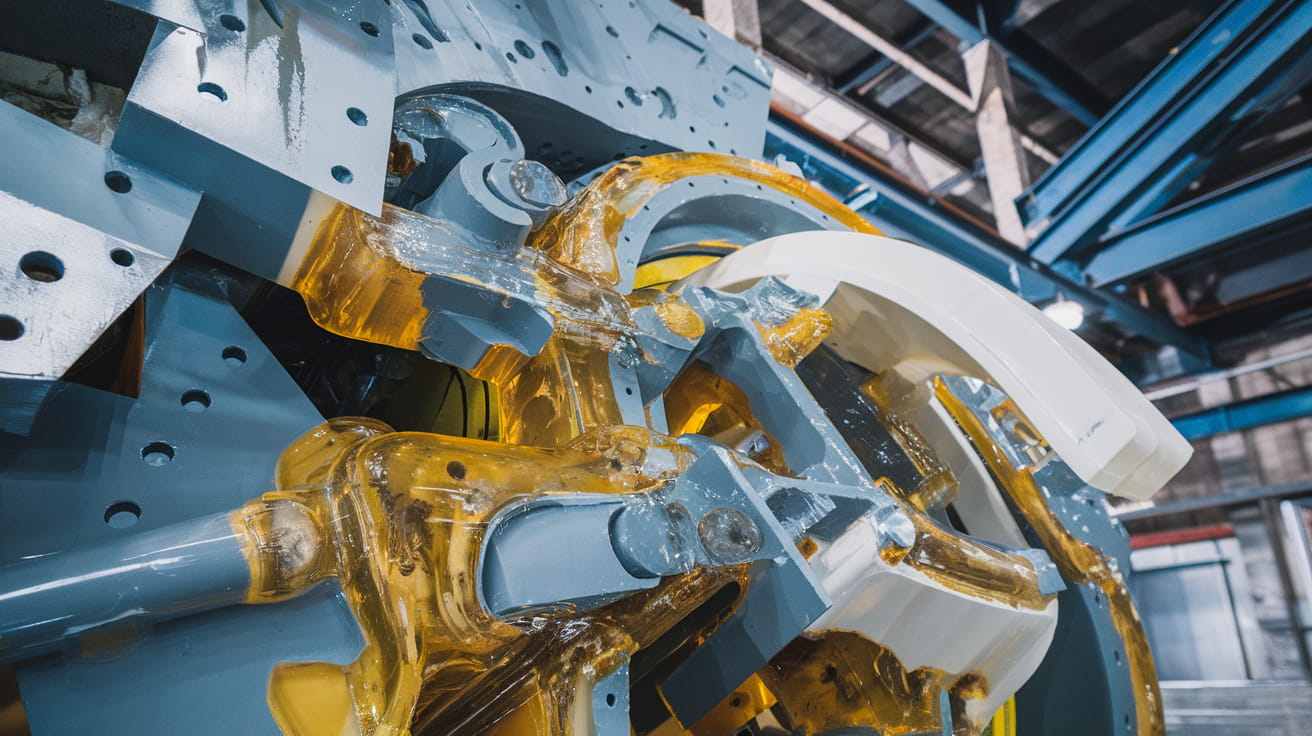
Industrial Adhesives
On the industrial side, epoxy resins are unparalleled as industrial adhesives. They work wonders in sticking diverse materials like metals, plastics, and even wood. They are a go-to for industries that require strong joints. In automotive manufacturing, epoxy adhesives hold vehicle components securely in place. In the construction industry, they make solid structural bonds. You’ll often see epoxy at play in the aerospace sector too, where bonding strength is critical. These adhesives are trusted by professionals because they hold up under pressure, and that makes them perfect for high-stakes applications.
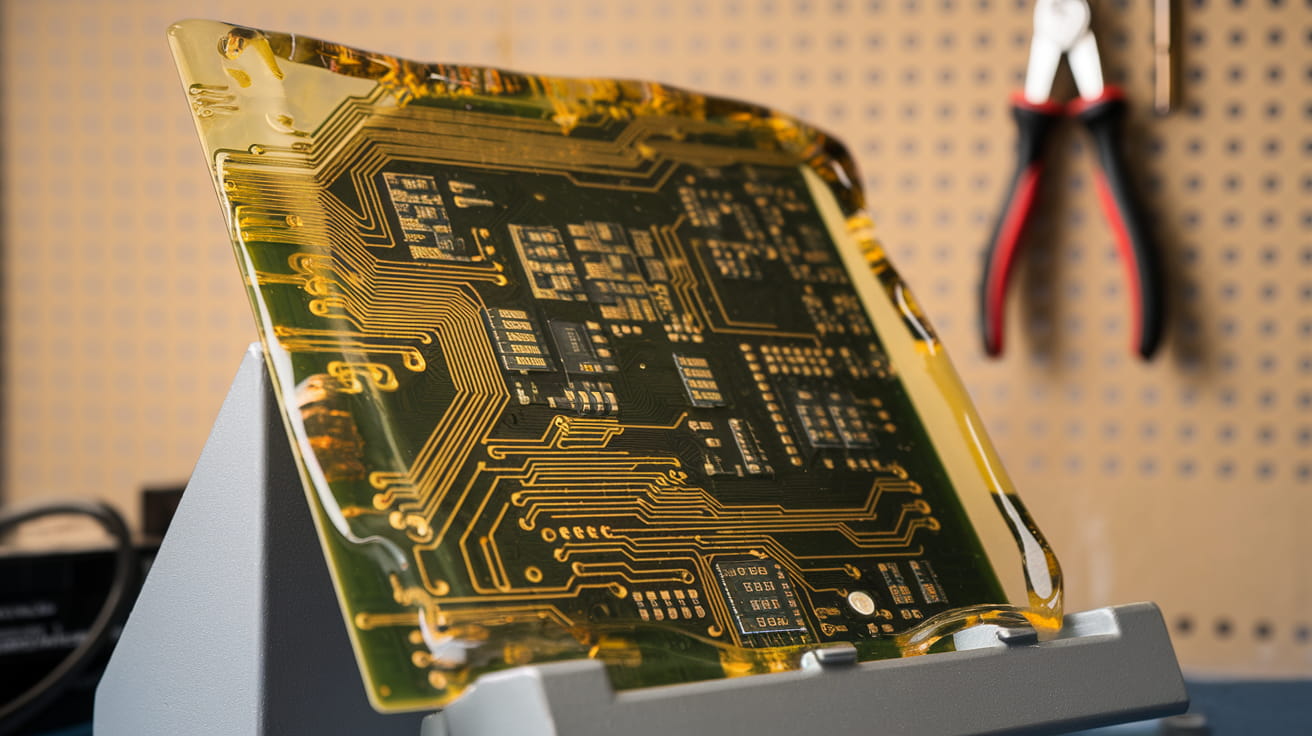
Electrical and Electronics Uses
In electronics, epoxy resins are a big deal. They offer insulation and protection, keeping components from moisture and dust. When working with circuit boards, epoxy coatings become part of the game, making things durable and keeping everything humming along. They are essential in ensuring electronics meet safety standards, so you can rest easy when using a device. In a technology-driven world, manufacturers lean on epoxy to make their products dependable. Be it for sealing electronic components or insulating them, epoxy resin is all but irreplaceable.
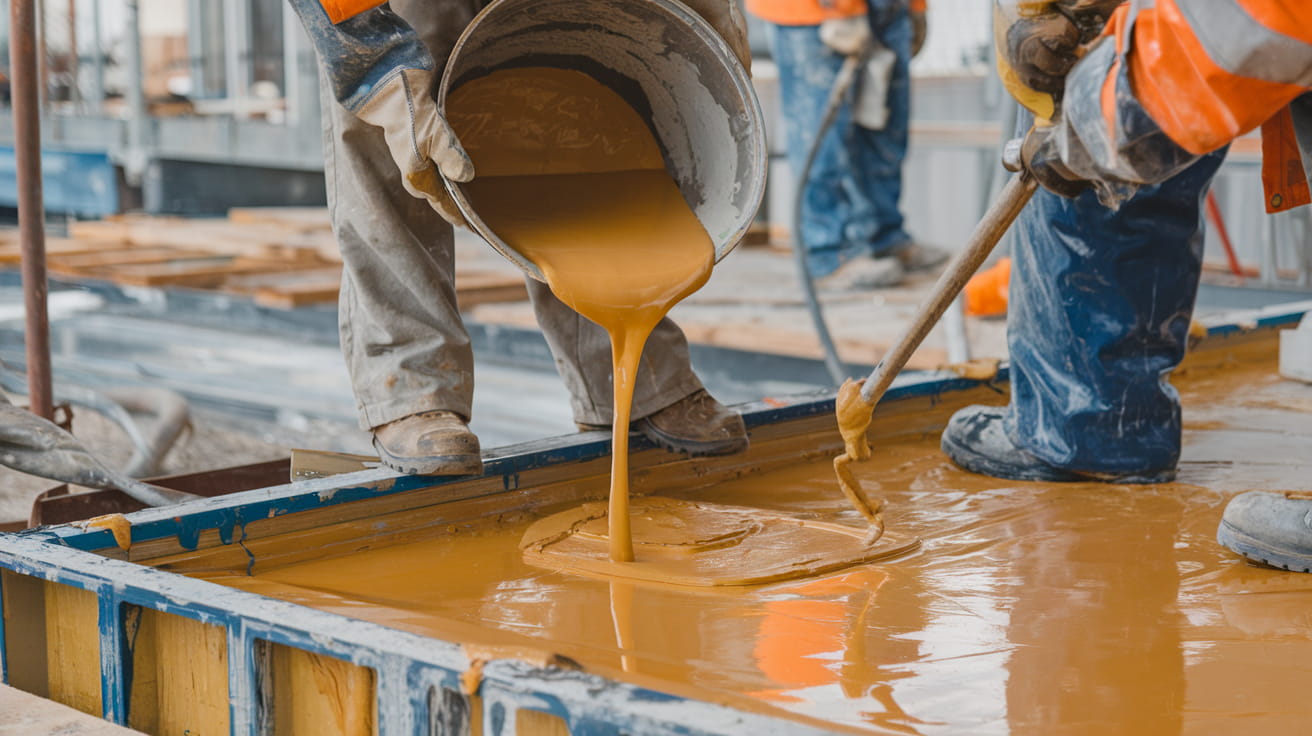
Construction and Building Applications
In the world of construction, epoxy resins are like heroes. They bond and seal tightly, forming protective layers on building materials. Epoxy coatings are well-known for their ability to resist wear, which makes them an excellent choice for flooring and structural applications. They are placed near high-traffic areas where durability is essential. Successful projects have used epoxy systems to enhance both longevity and appearance. They’re also useful in waterproofing, keeping water damage away. Builders rely on epoxy to deliver quality and reliability in every project.
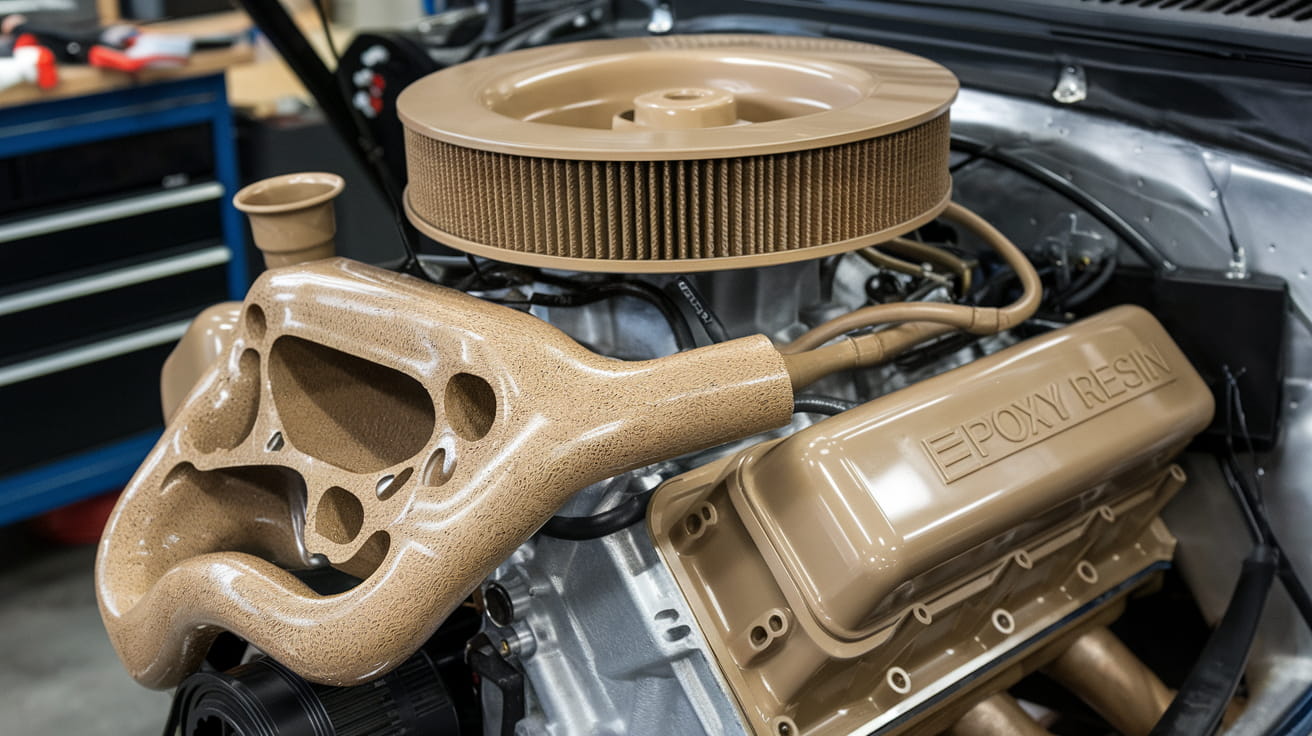
Automotive Industry Uses
The use of epoxy resin in automotive manufacturing is nothing short of revolutionary. With these resins, you have strong adhesives for parts assembly; they’ll make cars safe and sound. For over 30 years, epoxy-based coatings have dominated the industry with unparalleled corrosion protection. They help vehicles stand the test of time by fighting back rust. Automotive design innovators are using epoxy to manufacture lighter components without compromising the necessary strength and still manage fuel economy. It essentially makes life easier for car makers wanting to push the envelope.
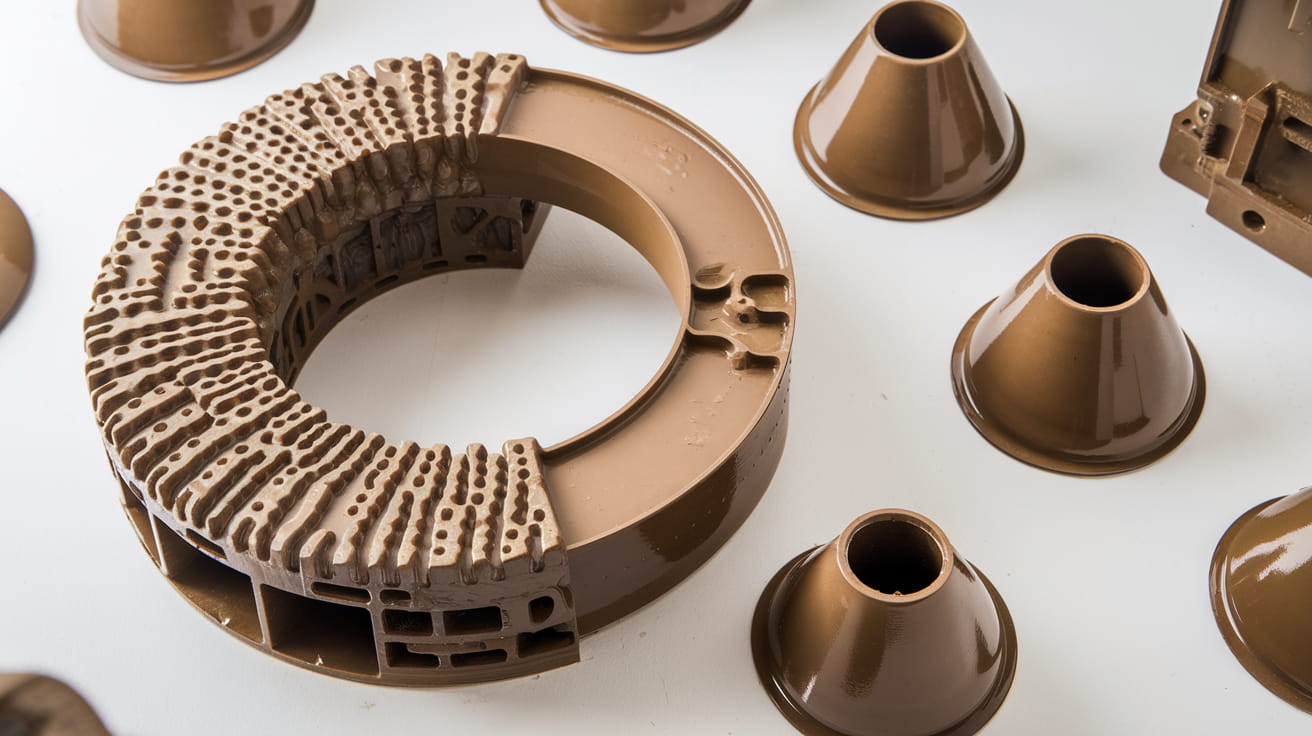
Aerospace Applications
Epoxy resins are important in aerospace engineering, where the lightweight composite materials used in aircraft are made. These materials must be strong and durable, capable of withstanding the rigors of flight. Epoxy makes sure they are. Examples include aircraft wings and fuselage parts that rely on epoxy for their superior strength-to-weight ratio. In an industry where every ounce matters, epoxy resins play a crucial role in achieving the perfect balance between durability and weight. It’s this innovation that makes air travel safer and more efficient.
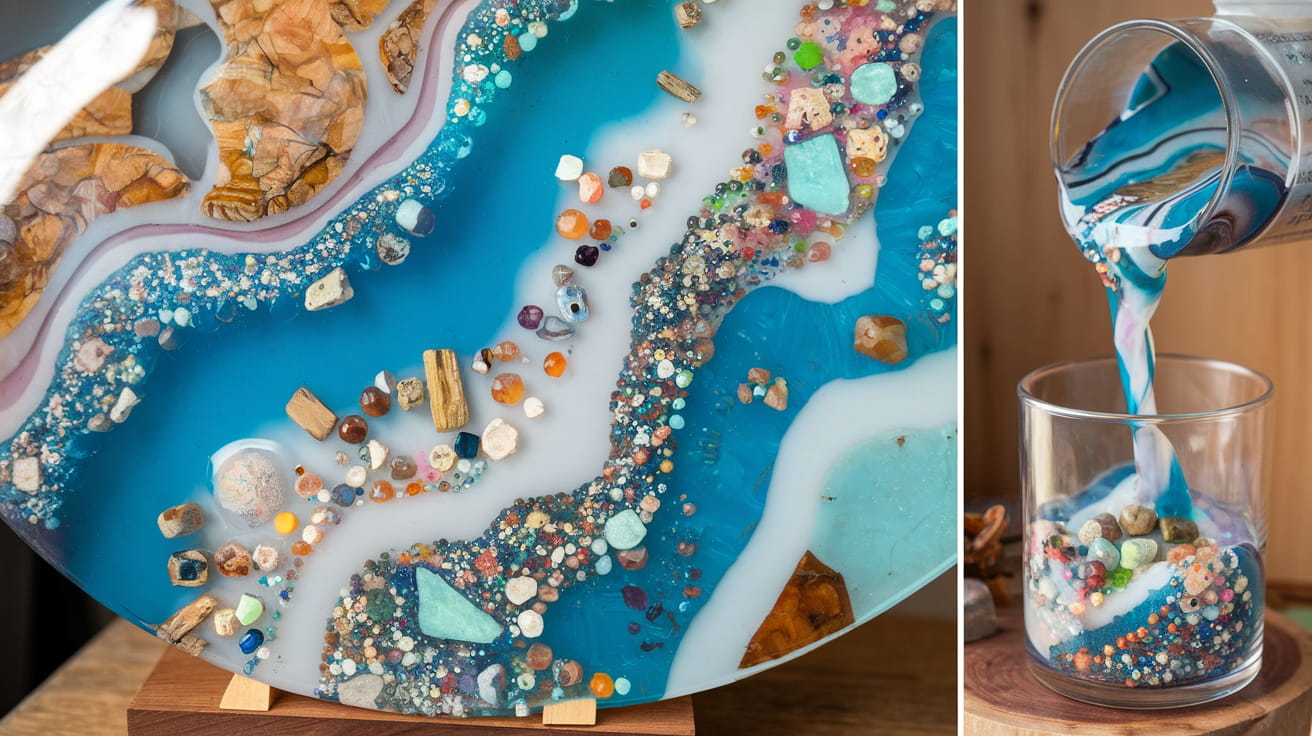
Artwork and DIY Projects
Epoxy resin has become a darling in art and DIY circles. Its versatility allows creators to make beautiful jewelry, unique tabletops, and striking decorative items. Artists love epoxy for its ability to mimic glass, offering a glossy, clear finish. For novices, the prospect of launching an epoxy project can be both exhilarating and daunting. Tips include working in well-ventilated areas and mixing colors thoroughly for the best effects. Crafters love it for adding a personal touch to their projects.
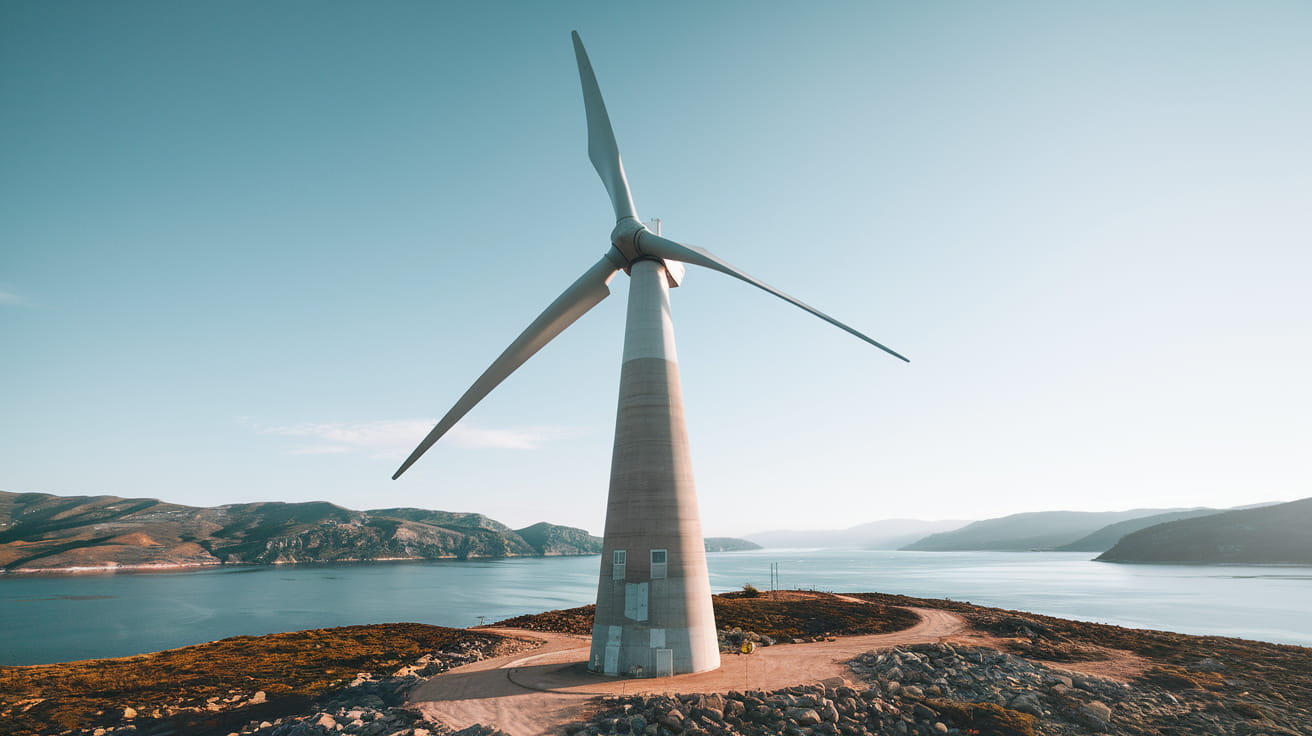
Renewable Energy Solutions
Epoxy resins play a large role in renewable energy technologies. They’re also vital in making wind turbine blades, which need to be sturdy and strong. Epoxy is also used in solar panels to stand up to the elements. Wind energy components account for a sizable portion of the epoxy market. Innovations in resin formulations are driving energy efficiency. Epoxy’s resilience makes it a go-to for outdoor applications, where maintaining performance over time is crucial.
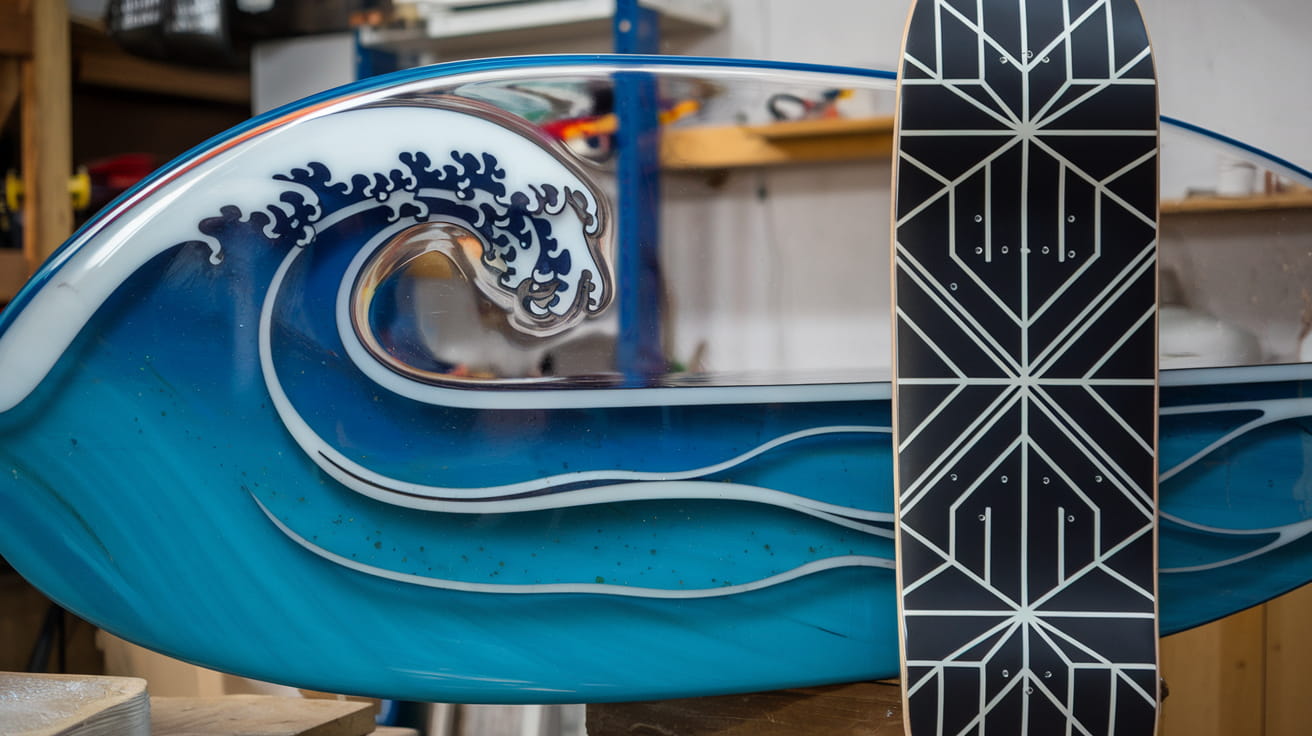
Sports and Leisure Products
Epoxy resins make their mark in sports equipment manufacturing. They’re used to create gear that’s tough as nails and light as a feather, ideal for high-performance sports. Think bicycles and tennis rackets, where every ounce matters. Epoxy coatings layer on extra protection for recreational products, so they endure longer. Many sports items, including surfboards and skis, depend on epoxy technology. This innovation gives athletes the confidence to perform at their best in their respective sports.
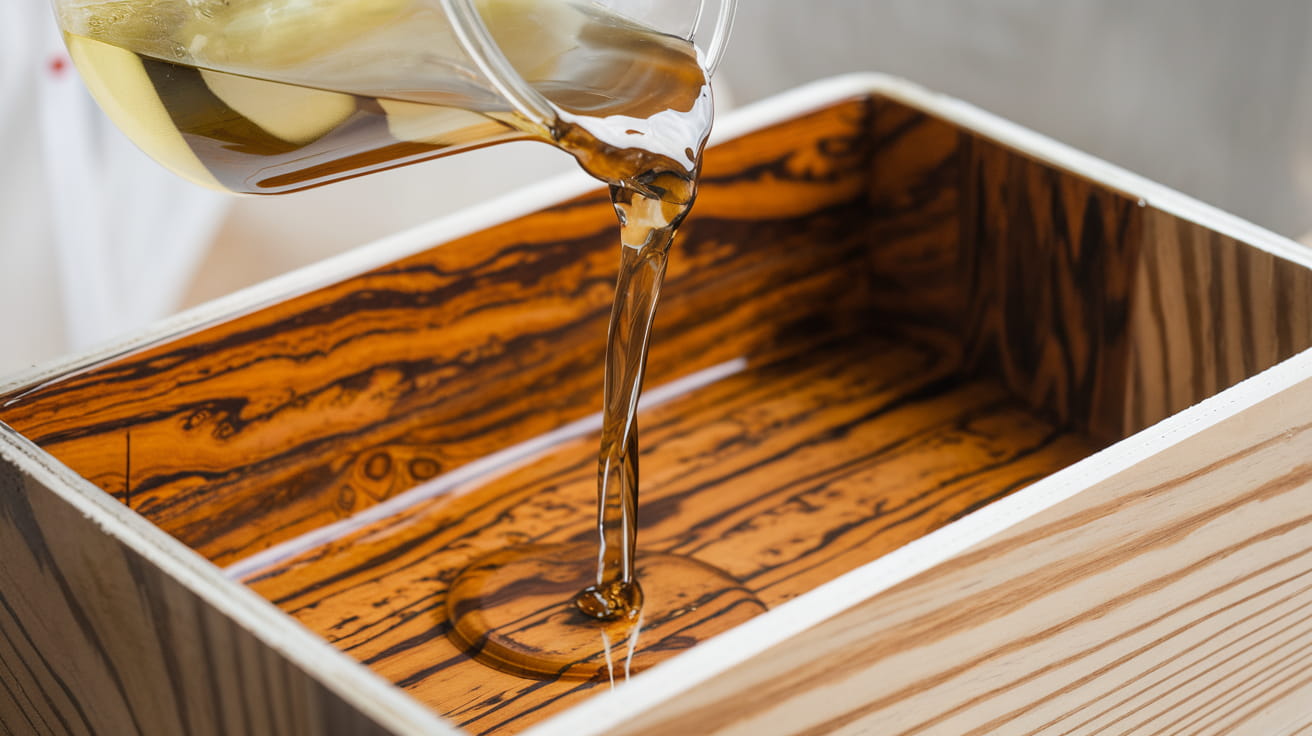
Food Packaging Solutions
Epoxy resins are integral to food packaging, providing barriers that extend food shelf life. These resins ensure packaging is safe; they have to comply with stringent safety guidelines. Products such as canned goods and beverage containers use epoxy to keep contents fresh. It’s all about maintaining the integrity of food. Epoxy resins easily find the right balance to keep consumers safe.
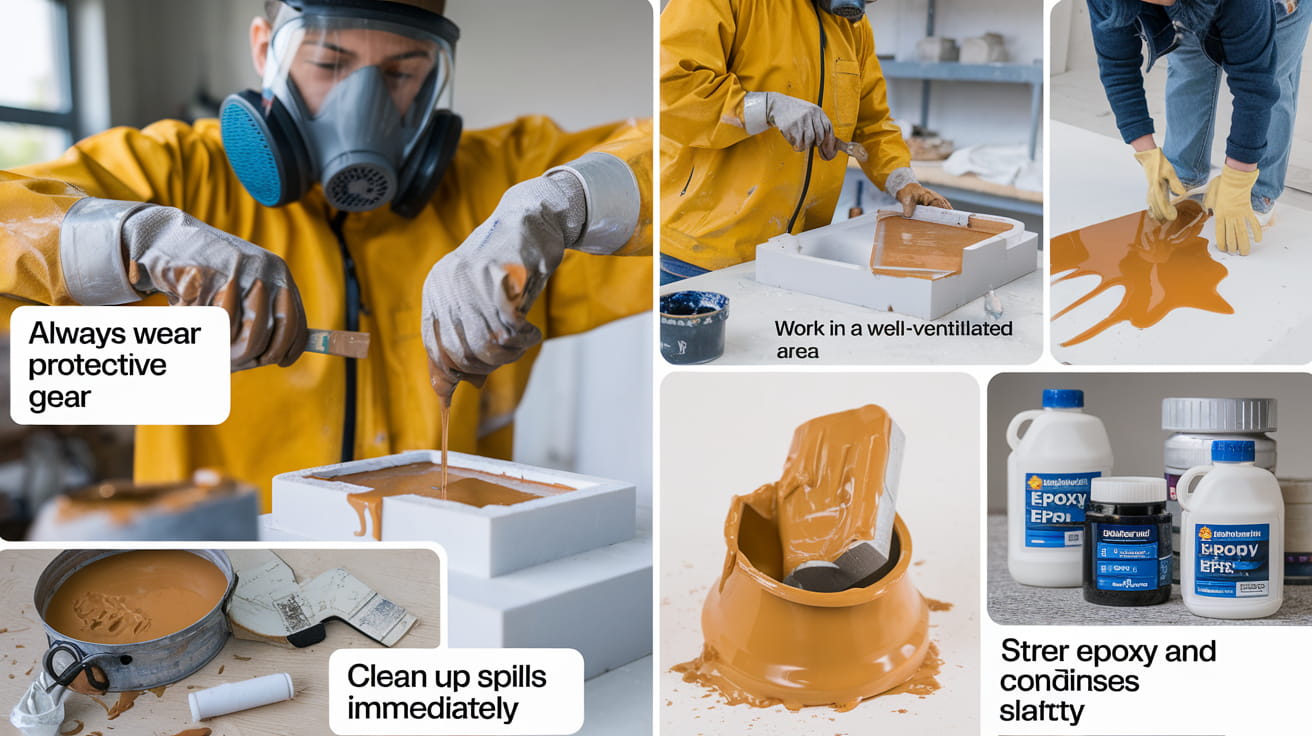
Safety Guidelines for Epoxy Resin
Handling and Storage Tips
When it comes to storing epoxy resin, it must be cool and sealed. Store your resin and hardener in their original containers with tight-fitting lids. Cool, dry, dark places are best to ensure the material stays stable. For example, a basement works or a storage closet. Keep in mind that heat and light can break down the resin and hardener, which can compromise their effectiveness.
Handling uncured epoxy materials takes some care, too. It’s important to wear gloves to avoid skin contact, as epoxy can irritate the skin. Take caution; latex gloves aren’t ideal for this scenario as they do not offer complete protection. Instead, opt for nitrile gloves for additional protection. Take note of the shelf life of your epoxy products. Most resins have a shelf life of around 12 months. Look for the ‘conform to ASTM D-4236’ designation on the label to be sure your epoxy is safe to use.
Protective Gear Recommendations
When working with epoxy, protective gear is your best friend. Gloves, goggles, and masks are essentials. Nitrile gloves are a good option since they offer better protection than latex. For your eyes, safety glasses are an easy and inexpensive way to protect them from splashes.
Masks are a necessity when working with fumes. You might need two different types: one mask with an organic vapor cartridge for fumes and one for dust. A NIOSH-approved respirator is your best bet for managing fumes. An N95 or KN95 respirator is also advised during epoxy work. Remember, comfort is key, so make sure your gear fits properly.
Ventilation and Workspace Safety
Good ventilation is a must when working with epoxy. Poor air quality can have serious health risks. Open a window or two to create circulation. You might also utilize fans to circulate air. Set up your workspace with proper ventilation to minimize exposure to harmful fumes.
To keep a safe environment, make sure that your work area is clean and free from obstruction. This limits accidents and makes your job easier. Remember that 90% of resins do not require a respirator. It’s better to be safe than sorry, so wear one, just in case.
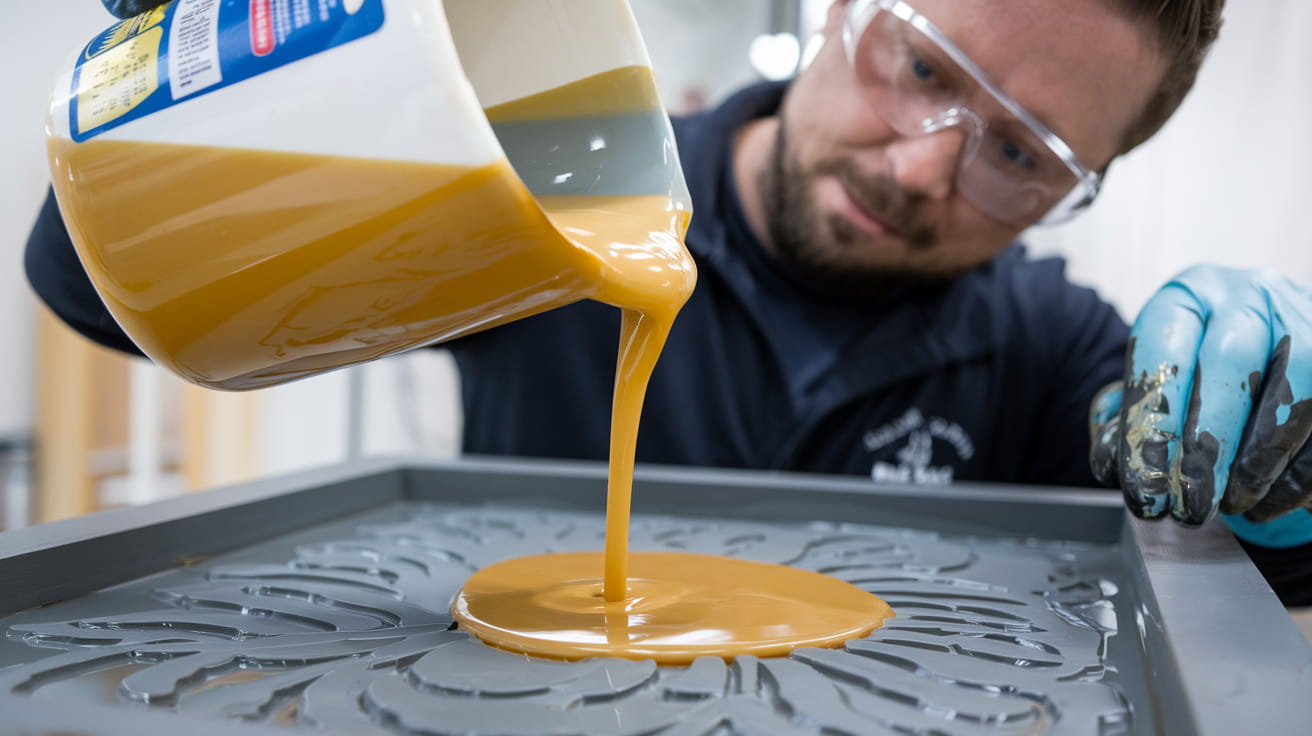
Mixing and Curing Epoxy Resin
Mixing Techniques
When you’re mixing epoxy resin, getting the right mix ratio is super important. You typically see a 2:1 ratio, meaning you need to mix two parts resin with one part hardener. There are two main ways to measure this: by weight and volume. Each has its pros and cons, but using volume is often easier for most projects. It’s like getting the batter right before you bake your cake—nice and simple, right?
Now, let’s talk about how to actually mix it. It’s just to combine everything, so you only need to mix for about 2 to 3 minutes. Don’t use dirty tools or you might contaminate it. If you’re dealing with a small batch, it’s fairly common. Take it slow and steady. For larger batches, you’ll need a little elbow grease to mix thoroughly and avoid bubbles. Believe me when I tell you this, good mixing is the key to prevent curing issues later.
Curing Process Explained
Watching curing epoxy resin is like witnessing magic in action. The resin and hardener make cross-links, a tough polymer network, which gives your project longevity. Factors like temperature and humidity matter here. A stable environment, ideally between 70° F and 85° F (21° C to 29° C), is what you’re aiming for. Too hot, and you risk overheating and bubbling, especially if you’re working with layers thicker than ½ inch.
There are fast-curing and slow-curing epoxies. Fast ones are great when you’re in a rush, but slow-cure options often give you a stronger finish. Follow up on your project; this will allow you to adequately catch errors.
Optimal Conditions for Curing
When it comes to curing epoxy, temperature and humidity are your best friends or worst enemies. You need an environment that’s stable. If humidity goes above 60%, expect a tacky or cloudy finish. Below 40%, things can cure too fast, which may leave bubbles trapped or surfaces uneven. Change your environment to get better results; a dehumidifier or heater works wonders.
Avoid common pitfalls such as moving the project around too much or exposing it to drafts. These can interfere with the curing process in ways you don’t want.
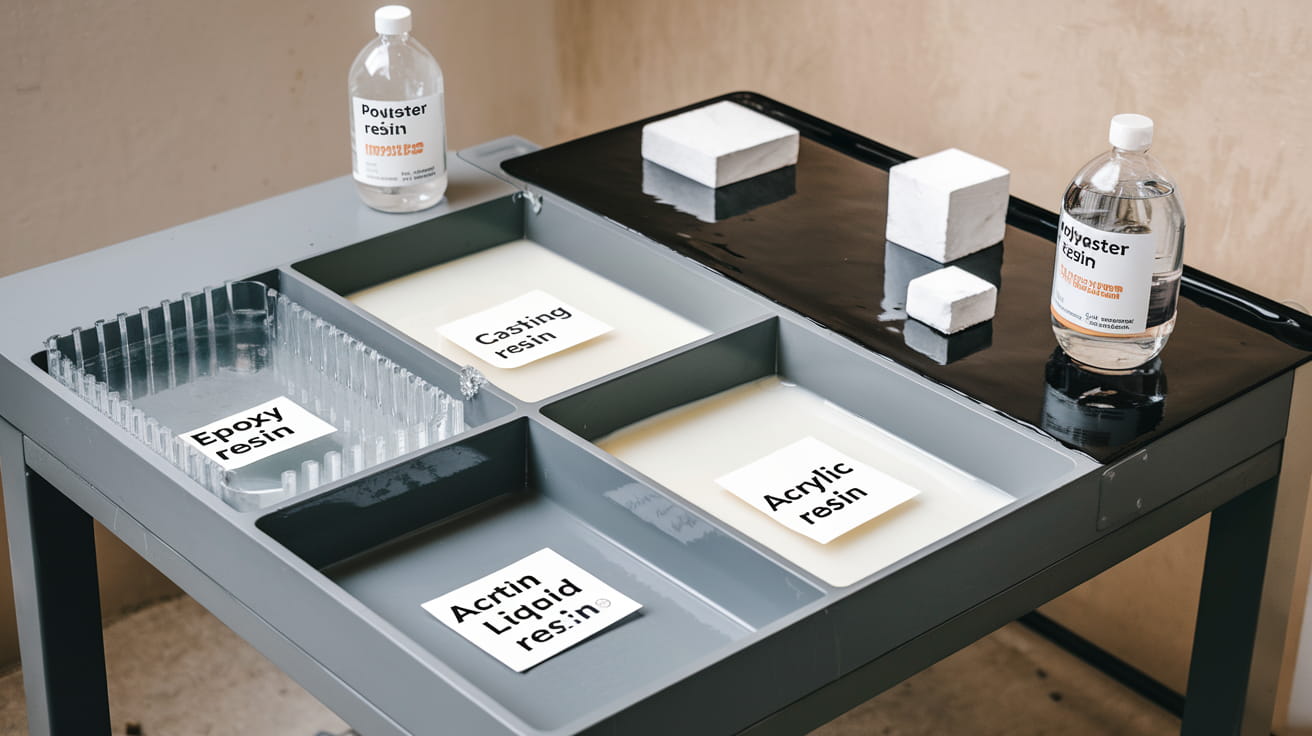
Comparing Epoxy Resin with Other Resins
Casting Resin vs. Epoxy Resin
Casting resin and epoxy resin serve different purposes. Casting resin works best for deep molds and embeds, like paperweights and decorative pieces. This is because it has longer curing times, which typically take 36 to 48 hours. This makes for a slower set, resulting in fewer bubbles and greater clarity and depth. Epoxy resin is revered for its rigidity and relatively fast curing time of 12-24 hours. This makes it perfect for coatings and surface layers.
Epoxy resins are unique because they cure through a chemical reaction between the resin and a hardener. This reaction can vary the working time and often gives you about 20 minutes to get everything just right. When selecting a resin for casting, the first thing to consider is the depth of your project. Epoxy is great for thin layers, requiring pours of only 1/8-1/4 inch at a time, whereas casting resins can handle larger volumes with varied mixing ratios, such as 2:1 or 3:1.
Acrylic Resin vs. Epoxy Resin
Acrylic resin differs from epoxy in several ways. This option provides excellent flexibility and cost-effectiveness. It’s ideal for budget-conscious applications, including art projects and DIY crafts. However, epoxy resin shines in areas requiring durability and strong adhesion, such as coatings or structural applications. Epoxy’s rigidity and excellent finish make it the choice for high-performance applications.
Acrylic is easier to use and cures more quickly, but it does not provide the long-term strength of epoxy. Which one you choose depends on what your project needs. For example, if you want a clear, shiny finish that stands up to wear and tear, look no further than epoxy. If you’re doing a budget-friendly project where rigidity isn’t as critical, acrylic could be the choice.
Polyester Resin vs. Epoxy Resin
Polyester resin is sometimes preferred for its cost-effectiveness and simplicity, especially in boat building or fiberglass repair. Epoxy resin provides superior adhesion and durability. This makes it ideal for projects that require strength, such as bonding or in high-stress environments. Epoxy’s two-part system—resin and hardener—provides a strong bond and superior durability.
In terms of cost, polyester resin may be appealing because it is less expensive. For applications that require long-term performance and structural integrity, epoxy resin’s advantages far exceed the slightly higher price. For example, epoxy is favored in aerospace and automotive industries, where reliability and endurance are non-negotiable.
Conclusion
The versatile wonder that is epoxy resin punches hard on a variety of projects. From fixing things to creating art, its uses seem limitless.
Think of a broken table top, now perfect and glossy; or a river table, with bright colours that beg you to stare. It’s magic, though, right? The resin shines, hardens strong, and lasts.
You can’t ignore all the safety stuff, though. Gloves, masks – they’re a must. Get it right, give it time, and bam – solid and smooth.
You have options here, and each one opens up new possibilities. So you’re excited to give it a try. Take the plunge and discover what you can create with epoxy resin. Start one today, feel its wonder.
Frequently Asked Questions
What is epoxy resin?
Epoxy resin is a versatile polymer. It’s known for its strong adhesive properties. It is used in construction, art, and electronics.
What is epoxy resin composed of?
Epoxy resin is made up of a resin and a hardener. When combined, they make a solid, strong substance.
What are the applications of epoxy resin?
Epoxy resin is used in flooring, countertops, and crafts. It’s also important in the electrical side for insulation.
Are there safety guidelines for using epoxy resin?
Wear gloves and wear masks, okay? Make sure there’s open ventilation. Avoid skin contact and inhalation.
How do you mix and cure epoxy resin?
Combine equal parts resin and hardener. Stir until smooth. For full hardness, allow curing for 24 to 48 hours.
How does epoxy resin compare with other resins?
Epoxy is more durable than polyester or polyurethane. It provides improved adhesion and chemical resistance.
Why trust epoxy resin for projects?
Epoxy, as a resin, is tried and tested. Its power and flexibility create an obvious choice for professionals everywhere.